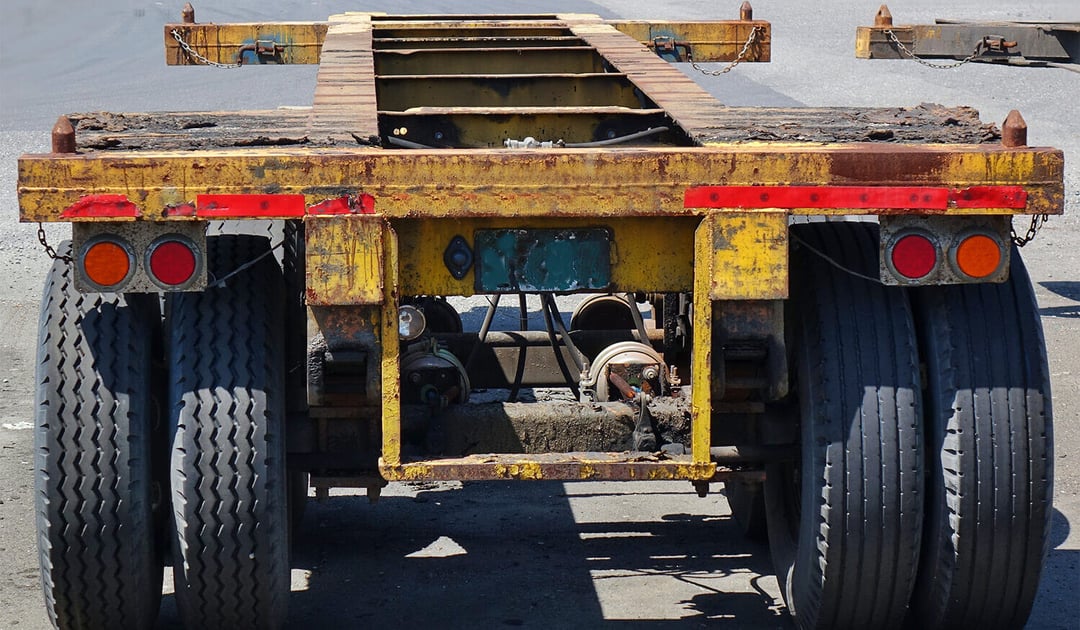
We often speak on how the linchpin to consistently high service levels of intermodal transportation service comes from dray. A subcomponent of dray that is an essential but often overlooked aspect of intermodal logistics is the chassis.
With that said, let’s take a deep dive into the complexities, challenges, and importance of chassis in the intermodal supply chain, which will help in addressing the important questions you should be asking when determining the best intermodal transportation solution for your company.
What Is a Chassis and Why Does It Matter?
At its core, a chassis is a wheeled frame used to transport shipping containers. While it may seem like a simple piece of equipment, the chassis plays a pivotal role in enabling the seamless movement of containers across rail, road, and port infrastructure. It serves as the linchpin that holds the intermodal drayage process together, ensuring that containers can move efficiently to their final destinations.
Without chassis, the movement of goods from ship to rail or truck—and eventually to the consignee—would literally grind to a halt on the ground. Despite their critical role, chassis are often misunderstood or taken for granted by those not directly involved in intermodal operations.
Understanding Chassis Pools
Chassis pools are collections of chassis that are shared among users within a specific market or terminal. These pools are designed to improve the availability and efficiency of chassis use, but they come with their own complexities.
Domestic vs. Marine Chassis Pools
Domestic Pools
These are primarily used for 53-foot containers and are simpler to manage. Companies like DCLI provide chassis for Class 1 railroads and other domestic freight movements.
Marine Pools
Used for 20-, 40-, and 45-foot international containers, also known as ISO containers, these pools are more complex due to varying rules, contracts, and agreements between steamship lines and intermodal equipment providers (IEPs).
Challenges in Managing Pools
- Balancing Supply and Demand: Ensuring that chassis are available where and when needed requires constant coordination between depots, rail terminals, and ports.
- Migration Penalties: Moving a chassis outside its designated pool or market can incur fees, as this disrupts the balance needed to serve all customers effectively.
- Accessorial Charges: Additional costs, such as split charges or repositioning fees, arise when chassis need to be retrieved or returned to specific locations.
Additional Charges Shippers Could Incur
Understanding potential costs is crucial for shippers to budget effectively and avoid unexpected fees.
Accessorial charges are often viewed negatively by freight buyers, as they’re perceived as penalties or unexpected costs. However, using the term “accessorials” in the context of intermodal shipping can be misleading and does a disservice to buyers. By definition, accessorials are charges that fall outside the scope of the initial pricing agreement.
In reality, some intermodal accessorial charges are predictable and necessary for every shipment and should ideally be included upfront in the pricing provided by your Intermodal Marketing Company (IMC). Gaining a clear understanding of what drives these charges is essential for effectively managing and optimizing your company’s intermodal budget.
Below are the most common charges associated with intermodal chassis:
Migration Fees
Shippers may face migration fees if a chassis is out-gated at one terminal and in-gated at a different location. These fees reflect the cost of repositioning the chassis to balance the pool.
Chassis Split Fees
A chassis split fee occurs when a trucker must retrieve a chassis from one location and the container from another. This situation often arises in port operations where terminals operate as "chassis-neutral" environments, requiring truckers to source chassis from depots before picking up containers.
Daily Usage Charges
Also known as per-diem charges, these fees apply when shippers or motor carriers keep chassis beyond the allowed free time.
Maintenance and Repair (M&R) Charges
If a chassis is returned in damaged condition, the shipper or motor carrier may be held liable for M&R fees.
Storage Fees
Storage fees may apply if a chassis is left idle for an extended period at a terminal or depot.
Fuel Surcharge
When repositioning chassis between markets, fuel surcharges may be included in the cost, especially for long-haul moves involving stacked chassis.
Premium Lease Fees
Some providers offer premium lease options for shippers requiring guaranteed availability.
Detention Fees
If a trucker exceeds the allocated time for loading or unloading a container, detention fees may apply.
Wheeled vs. Grounded Intermodal Operations
Another important distinction in intermodal logistics is the difference between wheeled and grounded operations within the intermodal ramp network:
Wheeled Operations
In wheeled operations, containers remain mounted on chassis and are ready for immediate pickup by motor carriers. This approach prioritizes speed and efficiency, allowing truckers to hook and haul the container with minimal delay. However, wheeled operations require significant space for parking and storing containers on chassis, which can be a challenge in high-volume or space-constrained areas.
Grounded Operations
Grounded operations involve stacking containers to optimize space, particularly in congested port environments. While this approach increases capacity, it requires additional lifts to move containers from stacks onto chassis. Truckers may also need to wait longer for their containers to be lifted and mounted.
Hybrid Models
Many terminals, especially in major hubs like Chicago, employ hybrid models that blend wheeled and grounded operations.
Pros and Cons of Each Model
- Wheeled Operations: Faster for truckers but space-intensive.
- Grounded Operations: More space-efficient but may involve longer wait times for truckers.
- Hybrid Models: Strike a balance between efficiency and flexibility, depending on terminal infrastructure and demand.
Innovations and Solutions in Chassis Management
To address the challenges of chassis availability and efficiency, companies like DCLI have invested heavily in new technologies and strategies:
- GPS Tracking
DCLI recently announced that it is equipping its entire domestic fleet with GPS technology, offering real-time visibility into chassis location and availability. This innovation addresses a longstanding challenge in intermodal visibility, particularly given that much of the drayage capacity comes from small operators who often lack the resources for advanced technology. By bridging this gap, DCLI eliminates the reliance on manual call checks, streamlining operations and improving overall efficiency in the intermodal supply chain. - Rollover Technology
By identifying defects when a chassis enters a rail facility, rollover technology ensures that equipment is repaired promptly. - Maintenance and Repair (M&R) Programs
Centralizing maintenance at depots ensures that chassis are in good working order, minimizing downtime for motor carriers.
Addressing Chassis Shortages and Preparing for Surges
The pandemic highlighted vulnerabilities in the intermodal system, particularly regarding chassis availability. Factors like increased container dwell times and surges in import volumes strained the industry’s capacity.
Today, however, the industry is better prepared:
- Street dwell times have returned to pre-pandemic levels, averaging around 5.5 days.
- Over 80,000 additional chassis have been added to the marine pool since 2020.
- Innovative programs, like DCLI's premium daily lease options, offer motor carriers greater flexibility in managing their equipment needs.
The Underappreciated Intermodal Chassis
Chassis may not be the most visible component of intermodal logistics, but they are undeniably one of the most critical. As Abby Anderson aptly put it during a recent podcast on chassis, "Chassis are the glue that makes intermodal possible."
By understanding the role of chassis, the complexities of managing them, and the potential charges involved, shippers can better navigate the intermodal landscape and optimize their shipping operations. Transparent communication with intermodal providers and proactive planning are key to minimizing unexpected costs and ensuring seamless delivery.
For more insights on intermodal logistics, subscribe to the Intermodal Logistics Podcast. Whether you're a seasoned logistics professional or new to the industry, understanding the intricacies of chassis management will enhance your ability to navigate the ever-evolving world of intermodal shipping.
Our team is here to help you make the best choice for your logistics needs. We'll work with you on flexible solutions that fit you best. For more information about InTek, or logistics and supply chain issues in general, check out our Freight Guides.
Get Updates
Featured Articles
Categories
- Freight & Shipping Costs (55)
- Freight Broker (66)
- Freight Forwarder (3)
- Intermodal Transportation (195)
- International & Cross Border Logistics (43)
- Logistics & Supply Chain (435)
- Logistics Service Provider (79)
- LTL (39)
- Managed TMS (49)
- News (40)
- Supply Chain Sustainability (12)
- Transportation Management System (37)
- Truckload (123)
- Warehousing & Distribution (51)